Trionic 7 C900 Conversion - Phase 1
The Idea
When the idea was broached to convert a classic 900 to Trionic 7 instead of the usual Trionic 5 flavor, I probably said something like, “The added complexity is probably not worth the extra effort and difficulty to tune”. I’m not wrong. However, helping a friend do some troubleshooting on his 9-5 and digging into TrionicTuning.com, a forum dedicated to the reverse engineering of the Trionic ECUs, I find Trionic 7 has come a long way in the last five years. New features, hacks, and abilities have made Trionic 7 even more powerful than before. The possibility to use its advanced features on other vehicles other than the original 9-3 and 9-5 got the cogs turning. I distinctly remember the mental exercise while driving the car thinking about what stuff could stay and what would need to be changed to do the T7 conversion from the T5 installed on my 1992 900. I thought about whether the existing flywheel and crank position sensor would work, that the injectors had the same flow rate, and that even the ECU connector was the same, so maybe pins could be shuffled around. When I got home, I spent an hour on SAAB WIS (Workshop Information System) reviewing each component to see if it seemed like it would be compatible or would need to be changed, how each part worked within the system, and what was absolutely necessary (or not) to make this happen. I wanted to do it, but I also wanted the ability to undo it, if I got stuck on the software side or just didn’t work as well as Trionic 5 has.
My daily ‘90 900T was converted to T5 at least a decade ago and it has been reliable and a great performer. I didn’t want to do major surgery removing or modifying parts that would leave me committed if this was a failure. I had enough experience with T7Suite (albeit a little rusty) and the overlap with T5 and EFI tuning systems certainly helped make it seem like a very doable task. I had heard of one other European individual who had done this conversion, but you never really hear about the problems or complications that arise. Knowing it’s seemingly possible (and not all that much effort on the hardware front) made only more questions. Would the car drive significantly differently than Trionic 5? Is there any real-world advantage? What kind of features can be implemented in the standalone configuration? Only one way to find out.
T7 Background
A brief synopsis of what makes Trionic 5 and Trionic 7 so different is necessary to understand why T7 may have some advantages and why it needs different stuff to operate. At its core, Trionic 5 is a “Boost” request system while Trionic 7 is a “Torque” request system. Whereas boost is the means to an end, when you put your right foot down, torque is what you’re after. A main addition to T7 over T5 is the electric throttle body. The throttle cable, controlled by the driver, is now decoupled from moving the throttle plate that allows the engine to breathe and make power. Although cleverly packaged, the movement of the throttle cable on the throttle body is merely a position indicator that sends information back to the ECU for interpretation and further action. Moving the throttle pedal requests more torque and the ECU figures out how much, and the best way to get there. It has two modes of adding torque, one is the throttle plate and the other is the turbocharger. T5, on the other hand, simply tells the turbocharger to target a certain level of boost at a certain rpm. It only has one move, add boost. There are several consequences to the electronic throttle body setup (ETS) which could be viewed as positive AND negative. Disconnecting the driver directly from control over the engine means there is going to be some delay between the input and the execution. Now this could be imperceptible milliseconds, but it still exists. There is also the issue of safety, since now if there is a component failure in the system the computer may be acting on bad information or no information at all. Of course, this was not overlooked by SAABs engineers and they implemented a clever design that reverts the system back to manual mechanical control in a “limp-home” mode if it detects a fault.
So what is gained with this computer-controlled throttle? A separate idle control valve is no longer necessary since the throttle body can control the throttle plate directly and make minor corrections to steady the idle speed based on temperature. Cruise control is also now directed from the T7 ECU, there is no separate control module, and no longer is there an entire vacuum system/pump that is piggybacked into the mechanical control of the throttle. This also means integrating cruise control on a car that never had it (like mine) should be very easy, but more on that later. Software functions that can change the characteristics of throttle changes are now available. The smoothness with which you interact with the engine can be increased by simply changing parameters; Kind of like a soft-close drawer. That mechanism that converts the non-linear motion of the throttle plate can be corrected to perform in a more linear fashion or dialed in to suit your own preference. This smooths the peaks and valleys of power delivery. With tuning abilities, you can effectively translate your human input into the most responsive engine output possible. Reduction in turbo lag is further improved as well as dialing your own flavor of engine response vs. smoothness. Trionic 7 also is an improvement over Trionic 5 in its sheer number of redundancies and promise of efficiency. A MAF (Mass Air Flow) sensor is re-implemented (just like back in the LH Jetronic days) but it also uses a MAP (Manifold Absolute Pressure) sensor, actually two, just as T5 does. Now each of these systems on their own is enough to run the engine, but together they not only provide that redundancy for diagnostic/reliability purposes, but they also compensate for each other's minor shortcomings. It is also significant to mention that while possible to tune Trionic 5 to run on a different fuel/mixture such as ethanol, it was never designed to be able to adapt on the fly like the later flex fuel “Biopower” T7 cars were. Thanks to the work of the TrionicTuning community this capability is available on all Trionic 7 flavors. In short, this means with some more clever engineering, you can fill up with E85 or E10 or straight gasoline and reap the benefits without worrying about what your actual mixture is and where you’ll have to stop next for the next fill-up.
Lastly, it shouldn’t be ignored that Trionic 7 was released in 1999, nearly a decade after T5 was put on paper. The added number of knobs and dials to turn is overwhelming and the level of abstraction on what the software is based on is a little mind-warping.
If this sounds pretty fantastic so far, then maybe you might be tempted to just jump the T5 ship and go straight for that T7 conversion. However, I still would argue that Trionic 5, the current support for it along with the ease of tuning, is Goldie Locks territory.
There were also a couple of compromises I decided I could live with. T7 has no analog Check Engine Light output. Again, if there is a problem, the dash is illuminated by the ECU sending the instrument cluster a CANBUS message. I can still check for codes using an OBDII scanner or hooking my laptop up to it, but I just don’t have the dash light. No big deal. Luckily there is a tach signal output on the ECU so the factory tachometer works just fine. There may be a couple of others that I’m forgetting, but nothing that was surprising or impactful.
The Conversion
The next step after the initial mental sign-off was to pull up SAAB WIS (Workshop Information System) which had the breakdown of all the T7 components and wiring. I came up with a plan of attack for each system and thought of what other caveats may be involved with implementation on a c900. I searched through TrionicTuning.com forums to see what was possible on the software side as that was the biggest unknown as Trionic 7 is much more heavily tied into the chassis where it communicates with other modules. Luckily, T7 is still under active development with new binaries being released with swanky new features and hacks for fun. Removing the immobilizer system and not having to integrate the instrument cluster which is normally the communication hub would be ideal. The release of open development binaries meant that T7 could be programmed on the fly which is something Trionic 5 has been able to do since the beginning.
ECU/Software:
Without getting in the weeds too much, this was the biggest unknown for me on whether this whole conversion would work or not. Trionic 7 requires a speed signal to operate, otherwise, it will limit performance in a major way. Typically the ECU would get a digital signal from the instrument cluster speedometer over the CANBUS. However, in early T7 cars that did not have ESP (stability control) system, an analog square wave signal, the same used in T5 (or C900 cruise control system), was utilized over one of the ECU pins. The trick would be to re-calibrate the number of pulses generated by the C900 ABS system to correctly calculate the vehicle speed. Other than that, removing the immobilizer function has been available for a number of years. The first step was to get the car running and ensure it could run without codes or limiters.
Wire Harness:
My first thought was that I could re-pin the ECU connector in my existing T5 harness, but I quickly changed my mind about that. Not only did I want to keep my working harness, in case I had to jump ship, it seemed like a better idea to mimic the factory implementation, wire colors, etc. This is where the added complexity really made itself known. T5 harnesses really have two wire junctions and two relays, T7 has many more redundancies and power management concerns so this increased to 4 relays and probably 5 or 6 wire junctions. Luckily, the wire lengths and setup for most wiring layouts were identical. Fuel injectors, coolant temp sensor, and DI Cassette sub-assemblies were all the same. Added to the layup were the MAF sensor and throttle body wiring.
Electronic Throttle Body:
Although the need for a mounting adapter was obvious, the throttle body is also the connection point to the engine from chassis-mounted components (like the intercooler hoses and throttle cable still needed) so its position needs to be in a relatively similar position unless you want to re-engineer all that stuff too. Two key things helped here - two different T7 throttle bodies were produced, one for the 4-cylinder models and one for the V6. The 4-cylinders were mounted vertically which caused the cable pull to operate at 90 degrees, however, the V6 version was mounted horizontally and this would put the pull action back to the same orientation. Worst case I would have to make a new throttle cable, but in the end, I was able to modify the mounting of the stock one which worked out great. For the adapter, I fired up my CAD and took a couple of scans/pictures of the mounting surfaces and where I wanted the throttle body to live. As luck would have it, a test fit with a 3D-printed adapter worked out perfectly with just enough clearance for the starter motor (phew!). I also tested my luck with a used eBay unit and after cleaning and resetting it so far has not disappointed. A couple of small modifications to incorporate the bypass return valve and we had a winner. 3D printing meant I could make some fairly complex geometry and smooth the transitions really well between the odd-shaped pieces. Using heat-set threaded inserts, compression sleeves, and high-temp nylon meant it should hold up to engine bay temperatures.
MAF:
Again besides an adapter to make it play nice with the factory airbox and complete the OEM look, the MAF is only 3 wires and relatively cheap. I purchased a new unit for this since I didn’t want to be chasing my tail on tuning issues when it is impossible to tell visually if the MAF is really good or not. Again the 3D printer was utilized with a couple different materials to best suit temperature, vibration and serviceability in mind.
MAF Adapter Time lapse
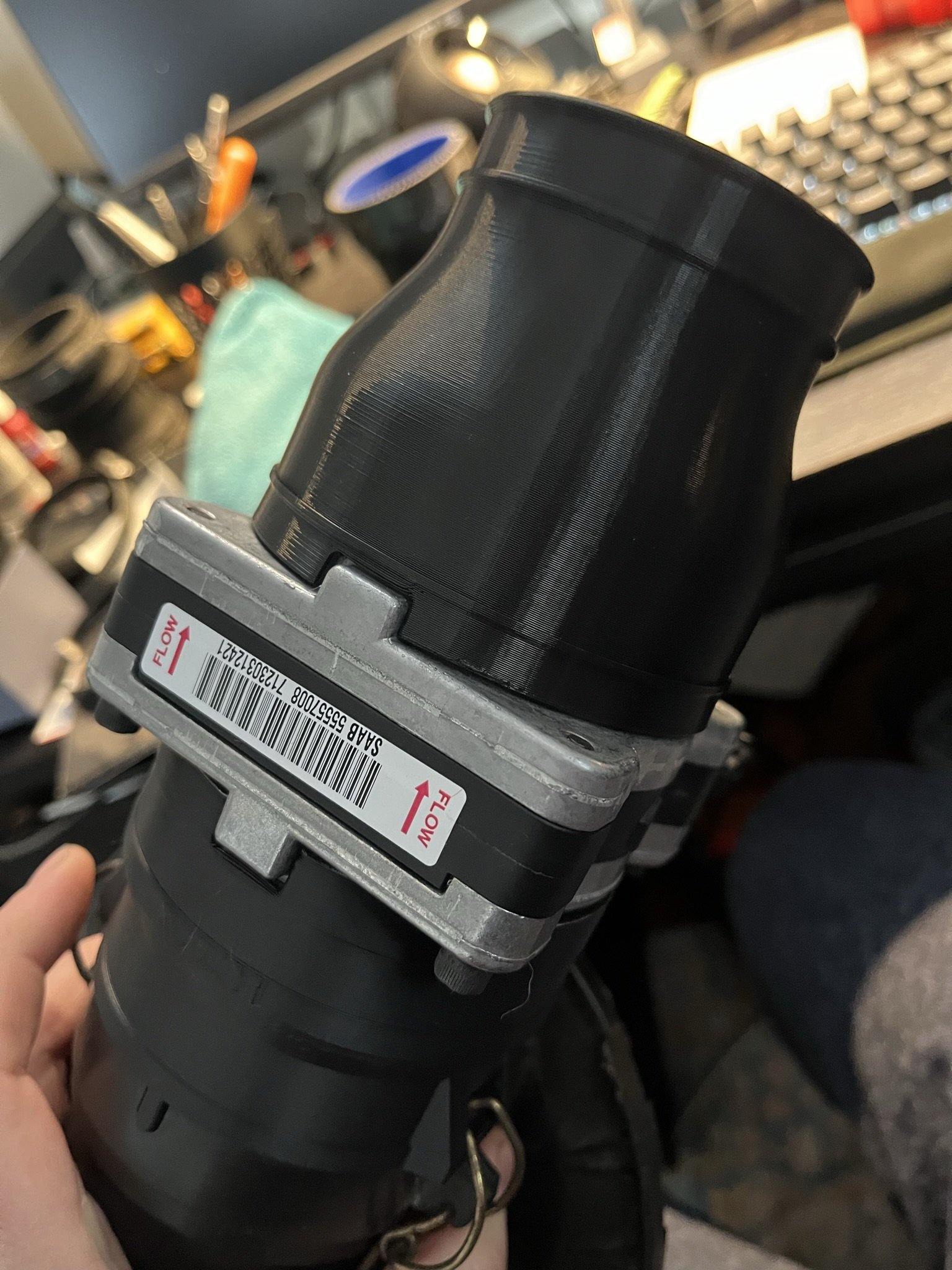

Fuel Injectors/Regulator:
This was perhaps the easiest part. Since all high-pressure turbos since 1994 use the same flow rate injectors, I decided to keep the Bosch -431s I already had installed along with the MCS 3bar fuel pressure regulator.
Idle Control Valve:
This goes away and leaves a couple of open ports in the manifold
Temp/MAP sensor(s):
Interestingly there were a few different sensors used over the years, but they all consolidated into a single combined temperature/pressure (TMAP) sensor. T7 actually uses two MAP signal readings, one pre and one post-throttle to detect issues with the bypass valve and again to add redundancy to the system. The temperature part of one of the sensors was only used in the pre-throttle body location so this is what I replicated. In the post-throttle body position, I built an adapter in my now open idle control port. For the pre-throttle position I created another adapter, this time out of machined aluminum that could be welded to an off the shelf 90 degree inlet elbow. The T7 throttle body having a smaller diameter meant it was a straight shot with standard couplers. The coolant temperature sensor specifications are still the same as the classic 900 original sensors so just match the harness with your original sensor.
Crank Position Sensor:
There was some question on whether a T7 sensor would be needed vs the T5 sensor since they ARE different part numbers in the OEM. However, the CPS kit I use in my T5 conversions uses an entirely different sensor more suited for the flywheel trigger pattern. The signal geometry between T5 and T7 is the same and I couldn’t think of a reason why it shouldn’t work, but this was still unknown. I had a backup plan if I did need to change sensors, but it turned out the T5 CPS setup works perfectly well.
Oxygen Sensor:
In Trionic 5 you can get away with using the stock 3-wire Bosch sensor because the heater resistance values are fairly similar. However T7 uses a different resistance heater element in its 4-wire sensor, so I didn’t even try to use the standard sensor. I would imagine it would throw a code for resistance out of range if you did.
Boost Control Valve:
It’s fairly standard now to use the T7 BPC valve in T5 conversions. I’ve moved on to using the T8-style valve which requires the same ECU modification but doesn’t suffer the same chattering the T7 valves do. So I just left this alone.
DI Cassette:
Probably the easiest swap of them all. A black DI cassette is a direct swap for a red one in this case.
Start!
So that was basically it, just swapping parts, and nothing needed to be modified to have that OEM look. Once in place I was able to figure out how to get the throttle cable positioned to the new cam arm and added a barrel-style cable end that would retain the cable properly. Finally, the only thing left was to try to start the thing up. To my surprise after just two cranks, IT RAN! … and then quickly died and did not restart (whomp whomp). It turned out that the program I used did not support the immobilizer delete function. After a bit of head scratching and forum searching I was pointed to a different base file to use and success after applying the patch. I was able to hook up the laptop and read all of the engine parameters. After some heat cycles and a couple of trips around the block, I buttoned everything up and prepared for my 700-mile trip down to Carlisle, PA for the annual SAAB show. Keeping tabs on the o2 sensor readings as well as putting the car through its paces I was thoroughly impressed with how well things just seemed to work. The MAF sensor which can more precisely measure the amount of air entering the engine does a perfect job of correcting for different engine setups. There are still some things to tune for and I believe running on T5 probably ran a little more boost. Tuning requires retraining your brain from boost numbers to air mass which is seemingly arbitrary, so that is still to come. My impression thus far though is that the turbo response does seem to be improved and perhaps has a more linear rate of acceleration. With more tuning and some more seat time I hope to be able to extract maximum benefit out of the system as well as learn a bit along the way. Phase 2 will also include utilizing the integrated cruise control system, so stay tuned!